化工管道伴热方式及设计要求 石油化工企业中的管道,常用伴热的方法以维持生产操作及停输期间管内介质的温度。它的特点是伴热介质取用方便,除某些特殊的热载体外,都是由企业的公用工程系统供给。伴热方式多种多样,适用于输送各种介质及操作条件下的工艺管道。通过几十年的实际运行,证实安全可靠。由于工艺管道内介质的生产条件复杂,因此选用伴热介质,确定伴热方式都应取决于工艺条件,现分析如下。 一、伴热介质 1. 热水 热水是一种不常用的伴热介质,适用于在操作温度不高或不能采用高温伴热的介质的条件下,作为伴热的热源。当企业有这一部分余热可以利用,而伴热点布置比较集中是时,可优先使用。有些厂用于原油罐或添加剂罐的加热,前者是为了节省蒸汽利用余热,后者是控制热源介质的温度,防止添加剂分解变质。 2.蒸汽 蒸汽是国内外石油化工企业中广泛采用的一种伴热介质,取用方便,冷凝潜热大,温度易于调节,使用范围广。石油化工企业中蒸汽可分高压、中压及低压三个系统,而用于伴热的是中、低压两个系统,基本上能满足石化企业中工艺管道的使用要求。 3.热载体 当蒸汽(指中、低压蒸汽)温度不能满足工艺要求时,才采用热载体作为热源。这些热载体在炼油厂中常用的有重柴油或馏程大于300℃馏分油;在石油化工企业中有联苯-联苯醚或加氢联三苯等。 热载体作伴热介质,一般用于管内介质的操作温度大于150℃的夹套伴热系统。 4.电伴热 电伴热是一种利用电能为热源的伴热技术。电伴热安全可靠,施工简便,能有效地进行温度控制,防止管道介质温度过热。 二、伴热方式 1.内伴热管伴热 伴热管安装在工艺管道(以下也称主管)内部,伴热介质释放出来的热量。全部用于补充主管内介质的热损失。这种结构的特点: (1)热效率高,用蒸汽作为热源时,与外伴热管比较,可以节省15~25%的蒸汽耗量; (2)内伴热管的外侧传热系数hi,与主管内介质的流速、粘度有关; (3)由于它安装在工艺管道内部,所以伴热管的管壁加厚。无缝钢管的自然长度一般为8~13米,伴热管的焊缝又不允许留在工艺管道内部,因此弯管的数量大大增多,施工工程量随之加大。 (4)伴热管的热变形问题应予重视,否则将引起伴热管胀裂事故,既影响产品质量,又要停产检修。 (5)这种结构型式不能用于输送有腐蚀性及热敏性介质的管道。一般很少用于石化企业工艺管道。 2.外伴热管伴热 外伴热管是目前国内外石化企业普遍采用的一种伴热方式,其伴热介质一般有蒸汽和热水两种。伴热管放出的热量,一部分补充主管(或称被伴管)内介质的热损失,另一部分通过保温层散失到四周大气中。在硬质圆形保温预制管壳中,主管与伴热管之间有一最大的保温空间,也就是伴热管放出的热量,几乎全部代替主管的热损失,因而这种型式的伴热保温结构,热源的耗量是最省的。 当伴热所需的传热量较大(主管输送温度大于150℃)或主管要求有一定的温升时,常规伴热设计将难以满足工艺要求,需要多管(伴热管根数超过3根)伴热。在这种情况下,应采用传热系数大的伴热胶泥,填充在常规的外伴热管与主管之间,使它们形成一个连续式的热结合体(如图1-1所示),这样的直接传热优于一般靠对流与辐射的传热。因此,一根带传热胶泥的外伴热管相当于用3根同直径的常规伴热管的作用。其结构如图1-1所示。
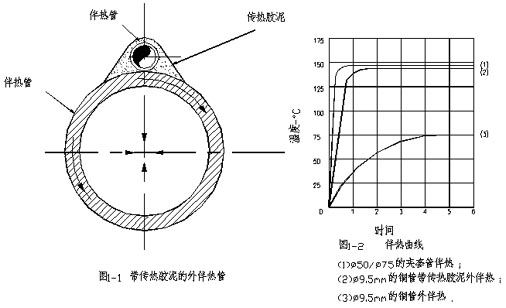
实践证明带传热胶泥的外伴热管可以代替投资昂贵的夹套管及多根伴热管。它能提供与夹套管一样的传热效果 如图1-2所示。 综上所述,外伴热管在石化企业中能广泛的应用,其主要原因有以下几点: (1)适应范围广,一般操作温度在170℃以下的工艺管道都可以采用。输送有腐蚀性或热敏性介质的管道,不能用内伴热及夹套伴热,但对于常规的外伴热管,只要在主管与伴热管之间用石棉板隔热后,仍可采用。 (2)施工、生产管理及检修都比较方便。伴热管损坏后,可以及时修理、既不影响生产,又不会出现质量事故。 (3)带传热胶泥的外伴热管,它的传热率非常接近于夹套管。同时传热胶泥能对任何部分维持均匀的温度。 (4)传热胶泥使用寿命长,具有优良的抗震能力。在加热与冷却交替循环的操作条件下,不会发生破裂、剥落及损坏现象。传热胶泥也可用于电伴热系统。 3.夹套伴热 夹套伴热管即在工艺管线的外面安装一套管,类似套管式换热器进行换热。在理论上只要伴热介质温度与内管介质的温度相同,或略高一些,就能维持内管介质的温度,这时蒸汽消耗量只要满足本身的热损失,因而伴热效率是比较高的。 常用的夹套管基本上分为两种类型: (1)管帽式夹套管 管帽式夹套管要求内管焊缝全部在夹套外侧。这种结构又称内管焊缝外露型,如图1-3所示。
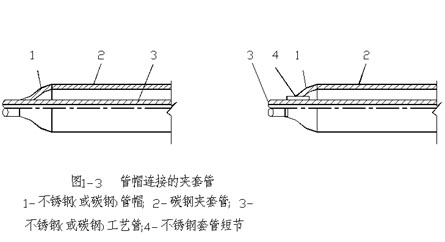
(2)法兰式夹套管 法兰式夹套管的内管焊缝全部在夹套内部,法兰及阀门处都能通过伴热介质,不会产生局部(指法兰及阀门处)热损失,达到全线在夹套下伴热的目的。这种类型又称内管焊缝隐蔽型。如图1-4所示。 夹套管伴热耗钢量大,施工工程亦大。但它能应用于外伴热管不能满足工艺要求的介质管道。如石化企业中输送高凝固点,高熔点介质的管道,需采用这种伴热方式。
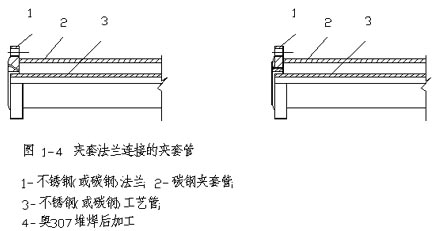
4.电伴热 以往管道伴热多用蒸汽作外供热源,通过伴热管补偿其散热损失。这种传统的伴热方式,伴热所需维持的温度无法控制;耗热量大,安装和维修的工作量大,生产管理不方便。采用电伴热可以有效利用能量,有效控制温度。电伴热方式有感应加热法、直接通电法、电阻加热法等。 在实践过程中,蒸汽外伴热管伴热是一种使用最多的伴热方式,故叙述蒸汽外伴热的设计原则,其它伴热方法参见其它有关规定。
三、设计要求 1.伴热设计的要求 (1)管道伴热设计,一般情况下仅考虑补充管内介质在输送过程或停输期间的热损失,以维持所需的操作温度,不考虑管内介质的升温。 (2)对于工艺有特殊要求,介质需要升温的管道,可以选用特殊的伴热方式进行升温输送。 (3)下列条件的管道应考率保温伴热。 a.在环境温度下,需从外部补充管内介质的热损失,以维持输送温度的液体管道; b.在输送过程中,由于热损失产生凝液而引起腐蚀或影响正常操作的气体管道; c.在操作过程中,由于在压力突然下降而自冷,可能导致结冰堵塞或管道剧冷脆裂的管道; d.在切换操作或间歇停输期间,管内介质由于热损失造成温度下降,又不能放空或扫线而影响下次输送的管道; e.在输送过程中,由于热损失造成降温,导致析出结晶体的管道; f.在输送高粘度介质时,由于热损失导致介质温降后粘度剧增,输送量下降且其量达不到工艺允许量一半的管道; g.在历年一月份平均温度的平均值低于0℃地区,保温管道扫线后仍有存水无法排净的局部管段。 2.伴热介质的选用 (1)管内介质温度在95℃以下的管道,应选用0.3~0.6Mpa的蒸汽作为热源。再伴热点(或称加气点)集中地段,也可选用热水伴热。 (2)管内介质温度在95~150℃之间的管道,应选用0.7~0.9Mpa的蒸汽伴热。 (3)输送温度在150℃以上的管道,当0.9Mpa蒸汽还不能满足工艺要求时,可选用热载体作为伴热介质。 (4)夹套管的伴热介质温度可等于或稍高于被伴介质的温度,但不宜高于被伴介质温度50℃。 3.伴热方式的选用 (1)输送介质的凝固点低于50℃的管道,可选用外伴热管伴热。 当有特殊要求且工艺管道的公称直径大于150mm时,也可选用内伴热管伴热。 (2)输送介质的凝固点从50~100℃的管道,或经常处于重力自流,或停滞状态的易凝介质的管道,宜选用管帽式夹套管伴369热,或带传热胶泥的外伴热管伴热。 (3)输送介质的凝固点高于100℃的管道,应选用法兰式夹套管伴热。管道上的法兰、阀门应带夹套型。 (4)输送腐蚀性介质或热敏性介质的管道,严禁使用内伴热管、带传热胶泥的外伴热管及蒸汽夹套管伴热。可选用外伴热管伴热,但伴热管与主管之间应有隔热措施。 (5)加热炉前的燃料气体,为了防止冷凝带液影响燃烧,可用夹套伴热。 (6)工艺管道要求在输送过程中有一定温升时,可选用带传热胶泥的外伴热管或夹套管伴热。 (7)对于在100℃左右或大于100℃时,管内介质易于分解、聚合或产生其它物性改变的物料,应采用热水外伴热管伴热,热水温度可根据工艺操作条件确定。 (8)输送有毒介质的管道当采用夹套管伴热时,应采用管帽式夹套管。
|